届いた箱を開封。
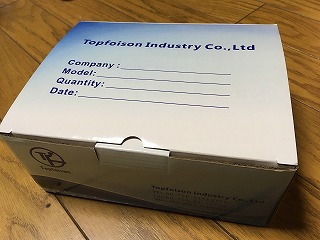
段ボール箱の中にこんな箱。
箱を開けると・・・
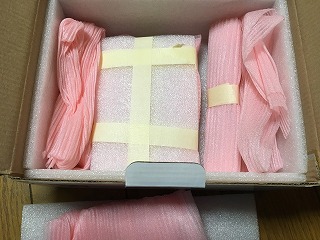
緩衝材。
箱が大きすぎるんでない?
緩衝材の中からお目当ての物を取り出して開封。
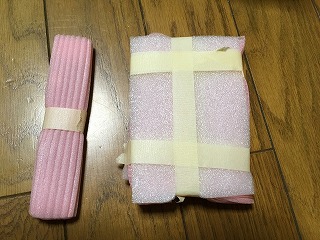

液晶パネルとコントロール基盤。
6インチで2Kなパネルには保護フィルムが貼ってあります。
とっちゃうけど。
基盤は十分小型。
USB,HDMI,イヤホン端子。
電源はUSBから供給するタイプで、PCで使う分には外部電源いらず。だそうです。
組み合わせるとこんな感じ。
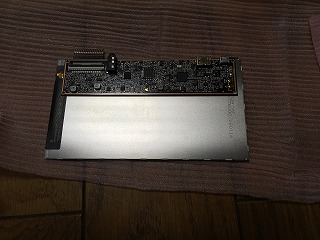
ケーブルをつないでくるっと背中合わせにできます。
でもって、いつもならばネットで使えそうな部品(ケースなど)を探して流用するのですが、ふと考えると、われらUMCには店長私物の3Dプリンターがあるではないか!とハタと思い付き。
今回は3Dモデルを作って3Dプリンターでケース作りにチャレンジ!
そうと決まれば
(この時点では印刷の許可を取り付けたわけではないですが)早速採寸。
仕事で使っているぼろぼろのノギスを引っ張り出してきました。
まあ、そこまでの精度で作るつもりはないので、ノギスでなくてもよかったのですが。
採寸データをもとに、まずは
2DCADで図面作製。
基盤とパネルの図面を書いたら、それを収めるケースも書き込んでいきます。
パネルの厚みが1.8mmだったので、納まる部分のへこみを2.8mmにし、パネルと基盤の間の壁を2mm。
基板部分はコネクタの厚みも考えて7mmとしました。
コネクタ部分がどうしても外枠より中に入ってしまうので、基板側は解放。
パネル側は押さえようの縁をつける予定。
できた図面をもとに
3Dモデル作成。
寸法を入れるとみずらくなるので、3Dモデルを作りながら必要な部分だけ寸法を入れることに。
ちなみにこの判断が
失敗のもとになるのですが…
3Dモデル作成に使ったのはWindows10に標準で付属している
"3D Builder"というソフト。
3Dは昔LightWaveを某Y氏に教わっていたので、ある程度感覚はつかんでいまして。
3D Builderは機能は大したことなさそうですが、寸法の数値入力など基本的なことは一通りできるようなので、あまりまごつかずに作成できました。
数値入力の際、
毎回全角文字に切り替わってしまう(全角で入力しても認識してくれない)のと、型抜きで穴をあけるときに何かの拍子に変な
ごみができてしまうのが問題といえば問題でしたが。
あと、この3Dソフトは.3mfという拡張子のファイルを作ってくれるのですが、店長さんの3Dプリンターは.STLのみ対応してます。
で、変換ソフトを探してみるもいくら探しても見つからない。
・・・・3Dソフトから直接STLを出力できることに気が付くまで
3日くらい悩んでしまいましたorz
さて、モデルが完成したんですが、店長さんのお店は私の家から車で45分ほど離れていますので、仕事の後でちょこっとというほど気軽にはいけません。
日曜はお店も休みだし。
とりあえず例会の時に印刷したいと店長さんに申し入れ、快諾を得られたので意気揚々と例会に出撃。
早速データを出力開始!
・・・え〜、
ものすごく時間がかかります。
1個当たり4時間弱くらい。
例会の時間ではモデル1個しか出力できませんでした。
店長さんにお願いして、2個目のデータを出力だけしておいて、帰宅。
翌々日、できたよ〜と連絡をもらったのですが、実際に取りに行けたのはそれから数日後…
で、できたパーツがこちら。
時間がなかったので、液晶を固定する
枠は割愛。透明なパネルでも購入することに。
パーツを受け取った帰りにホームセンターに寄り道。枠の材料やねじなどの部品を調達。
で、そろえたのがこちら。
透明パネルはPET樹脂製。
アクリルを使えば透明度が高くてよさそうなのですが、道具がない&
加工が難しそうなのでPETのパネルを選択。
透明度は問題なさそうだし、何より
カッターで加工できるのが魅力。
あとは基盤固定用のビスと枠の組み立て用のボルトナット。
基盤は長さ3o程度のビスが良かったんですが、なかったので一番身近いビス(それでも6o)を、ボルトナットはM2位を想定してたのですがこちらもなかったので一番細かったM3をそれぞれ購入。
材料もそろったので早速組み立て。
まずはパネルが収まる部分から確認。
ケーブルを出す穴の位置は良さそう。
大きさもまずまず。
で、はめ込んでみると…
測ったようにぴったり!(いや、測っただろ^^;)
実際には縦横は測定したサイズ+2oで、厚みは+1oで作成、がたつくようであればスポンジかなんかで固定しようかと思ってたのですが、必要なさそうなくらいのサイズ。
ひっくり返して
ケーブルの確認。
こちらも問題なさそう。
ちなみに穴とケーブルの中心がずれていますが、これは基盤固定用のビス穴が近かったから。
”穴なんか後で開ければいいじゃない”と思ったあなた。
3Dプリンターの場合、閉鎖空間部分は身が詰まっているわけではなく、ハニカム構造の
中空状態になっているので、あとから開口すると穴周りの強度が足りなくなります。
なので、開口部分は補強を兼ねてデータ上で穴をあけておくべきだと思います。
ということで、
基盤固定用の穴位置も確認。
穴ピッチもぴったりです。
気をよくして仮の位置合わせ・・・
ん?後ろのパネルの
切込みが小さいぞ?
3Dデータを作るときに、2Dデータをその都度測定しながら反映していったのですが、
1)全体の中心線を引く
2)中心線からの寸法を測定して半分作成
3)反転して残り半分を作成
・・・ってつくったんですよ。
実はケーブル位置の関係で基盤が中央部にいない
(上下はともかく、左右も微妙にずれている)のを
忘れてましてorz
まあ、ギリギリ
収まりそうだからいっか!
ちなみに、基盤固定用の穴もずれてました。中空ハニカム部分に穴をあけることにorz
気を取り直して先を進めます。
透明PETの加工。
アクリルより安く、加工がしやすいので、失敗したときのためにパネル2枚取れるサイズのものを購入してきました。
厚みは1.5o。
PET素材は柔らかいので、これくらいの厚みがないと曲がりそう・・・
加工方法はカッターですじを入れて折るだけ。
1.5o以上のパネルはアクリルカッターを使うように書いてありましたが、普通のカッターでも十分切れます。
この通り。
コツは”両面にすじを入れる”のと、”すじの深さはパネル厚みの半分以上”の2点。
一回ですじを入れようとせず、何回かカッターでなぞったほうがうまくいきます。
表と裏のすじがずれないように注意。
で、
固定用の穴あけ。
枠と重ねてマジックでケガキ、ドリルで穴あけ。
ただ、PETは柔らかいので・・
簡単に穴は開くものの、
バリが出ちゃいます。カッターでなるべくきれいにとっておきます。
で、基盤固定用の穴がほぼ埋まってしまっていたので
ドリルで拡張
ちなみにこの穴、データ上では2oで作成したのですが、ほぼ穴がない状態。
とりあえずビスを使う予定なので1oのドリルで開口。
この時点ではハニカム部には穴をあけていません。
状況によってはビスを直接打とうかと。
で、
ビス。
パネルの厚みに基盤の厚みを足しても3o程度しかないのに、6oの長さのビスではパネルを
突き抜けちゃう。
とりあえずビスで穴を広げておいて、使うのは・・・
手元にあったねじ。
何かの部品をばらした時に出てきたねじです。ちょうど4本あったのでこれを流用することに。
このねじはボルトと同じで太さが一定なので、さっきのビスで穴径を調整しておいて、その穴にねじを押し込みます。
ビスで開けた下穴にはドリル状の跡が残るので、これに引っ掛けるようにしてねじを締めこみます。
基盤にゆるみがないことを確認したら全体の組み立て。
裏側のパネルを当ててみると・・・
液晶の受け側パネルに
ゆがみが。
実は、3Dプリンターは出力後にゆっくり冷まして、冷めきってから台から外すのが正規の方法なのですが、時間がなかったので印刷直後
のまだ熱いうちにさっさと外してしまい、気が付いたら
全体的に歪んでしまっていまして。
お湯を沸かしたやかんを上にのせてゆがみを取ったのですが、角の一部はゆがみに加えへこみまでできてしまっていたのでこんなことに。
まあ、液晶面が平らだったので
気にしないことに。
でもって全部をボルトで固定しようと思ったらボルトが通らない。
全体固定用の穴も3oのデータに対して2o未満しかありませんでした。
買ってきたボルトが3oなので、そもそも通らなかったのかもしれませんが。
というわけでそっちの穴もドリルで拡張。
(写真はありませんが、電気ドリルで4oの穴を開けちゃいました)
全部開けるとこんな感じ。
開口部分の壁には1o程度の厚みがあるので、これくらい拡張しても中空部まで穴が開いたりはしませんでした。
ボルトが通るようになったので
全体を仮組。
裏面の基盤ですが、ケーブルが短くて長さがぎりぎりしかなかったので、一度外して、ケーブルをつないでから再度固定しなおしました。
無事ケーブルもつながったので本組立。
HDMIとUSBをつないで動作確認。
おお、
画面きれい!文字ちっちゃ!^^;
出来上がってみると、
思った以上にかっこよかったのでほぼ満足。
ただ、このままだと自立しないので足をどうしようか思案中…